Member Blog: Cannabis Extraction – Creating a Competitive Advantage Through Data
Marijuana Laws, Regulations, & Politics March 14, 2022 MJ Shareholders 0
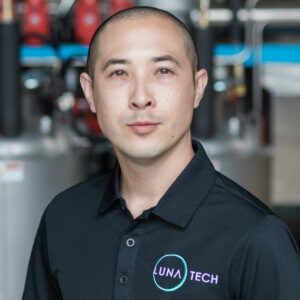
By Jack Naito, president and co-founder, Luna Technologies
As customers become more sophisticated and discerning about the fast-growing cannabis extract market, from vapes to dabs to infused pre-rolls, the need to routinely produce consistent, quality extracts at scale is becoming doubly important for processors. Compounding the issue, the potential for federal legalization will bring significant growth opportunities but also increased federal oversight, including the need for Good Manufacturing Practices (GMP) and other onerous standards that will challenge unprepared operators.
Future-Proof Extraction Operations Through Data
To overcome these twin challenges, processors should start developing (if they have not already) a framework to capture, review, and analyze data at every stage of production to produce consistent, quality, and compliant products.
That framework should examine every aspect of the extraction process, starting with the type of material harvested from farms, including how it is stored and handled, through to the final, packaged retail-ready product.
It should also be tied to specific goals and clear objectives. Capturing data simply to capture data within a given framework but without a clear idea of how that data will be used can lead to analysis paralysis, or worse, endless trial-and-error that wastes time and material, eating into expected profits.
Leverage Design of Experiments Methodology
Design of Experiments, or DoE, is a scientific methodology that can help guide processors in determining the key parameters they want to track and how those parameters interact. This starts with assertions that map to specific goals or objectives, such as investigating the yield of a specific terpene with the goal of blending it with a distillate-based vape cartridge. From here, processors can design and set up experiments with varying inputs from temperature to pressure, to biomass composition, all to understand how the yield of a specific terpene is influenced throughout a given process.
When these learnings are applied at production scale, the framework developed through DoE methodology provides a guide for creating consistent products, but also to better manage and rectify issues that may arise. With specific goals in mind, processors can then determine what data they need to capture and analyze.
The Four Steps of Data Capture
Step 1: Chemical Makeup – When selecting or determining what plant material to use for extraction, processors first must examine the chemical makeup of the cannabis biomass. This can include the profiles of cannabinoids, terpenes, and the fat/wax/water content.
The exact chemical makeup of cannabis biomass can be difficult to determine because of its nonhomogeneous nature. Imagine closing your eyes and selecting a random sample from a container of bulk biomass. Maybe you grab a sugar leaf or flower, high in THC-laden trichomes, or maybe you grab a fanleaf with little to nothing to contribute to a high-quality extract. The chemical composition will look significantly different depending on how one selects the sample. So it’s important to be cognizant of what and how biomass testing is conducted, and often a single sample isn’t the answer. Knowing the approximate chemical makeup of the feedstock material will guide the processor to determine what type of recipe they will use for extraction and post processing and, ultimately, what end products are most valuable for a given input.
Once the chemical makeup has been determined, the processor will know the inputs of the material, such as the associated THC, CBD, terpenes, etc. They can then use that data to determine what will (or should) come out of the extraction process at its conclusion. This is the mass balance of the production process. It is difficult or impossible to optimize any process if one doesn’t know exactly what goes in and what comes out. Of course, this is much easier said than done given the nonhomogeneous nature of biomass.
Step 3: Identify and Maintain Key Process Parameters – Depending on the recipe and desired end product as determined through the above steps, the extraction process will need to maintain specific temperatures, pressures, times, and flow rates, among other key variables, to ensure a consistent, quality product. This is where a DoE or other similar process can add significant value. Analytical tools, such as the DoE, can help determine what process parameters need to be precisely controlled, and what parameters can have looser controls or can be ignored altogether. Compliance comes into play here as well. The ability to track and record these key data points is crucial to achieving GMP compliance as well as creating a consistent product that customers expect.
Step 4: Post Process Review – In order to understand how recipe parameters affect the end product, the processor needs to know its chemical composition as well as the composition of any waste materials (e.g., biomass, fats, waxes), or impurities that have been filtered out. Capturing this data is vital as it offers the critical clues to why a particular batch did not turn out as planned, for example, so the processor can investigate potential causes and corresponding solutions.
Step 5: Recording Data Between Each Process – What happens between each process is nearly as important as what happens during the process. Storage conditions can have an impact on quality and consistency, issues that may not be readily evident within the data capturing during processing. Those data points to know, among others, may include monitoring the freezer temperature where biomass is stored, measuring the humidity of the environment, documenting when and how equipment is cleaned, or even tracking how long material sits between extraction and placement in a vacuum oven.
Decision Making Via Data Analysis
After the data is captured and analyzed, managers may need to enact decisions if the data shows deviations from the expected outcomes. For example, as part of post-production lab tests (step 4), are acetone traces appearing in the finished product? If so, the organization may need to change its equipment cleaning practices (step 5) to ensure unwanted trace chemicals are not seeping into finished products.
Although enacting a program to better capture, review, and analyze data can appear to be a daunting task, doing so will provide the processor a significant competitive advantage. Not only will it help ensure consistent production while future-proofing the organization against coming regulations, it may also enable processors to experiment with and develop novel or proprietary extracts derived from a repeatable, scientific method that can’t easily be replicated by competitors.
Jack Naito is President of Luna Technologies, where he oversees operations, strategic growth, and R&D for the company he co-founded in 2016. Jack entered the cannabis industry after time spent as a Materials, Process, and Physics Engineer for aerospace giant Boeing. Jack obtained an Economics and Business degree from Colorado College and a Master’s degree in Mechanical Engineering from the University of Washington.
Luna Technologies engineers state-of-the-art extraction equipment for cannabis processors. The meticulously designed, automated equipment empowers operators to process fresh-frozen or cured plant biomass with stress-tested hardware and built-in failsafes to foster a superior level of workplace safety while also lowering labor costs. Luna’s Earth-conscious engineering approach helps decrease energy consumption while setting the industry standard for safety, quality, consistency, and customization in support of creating clean, consistent cannabis concentrates with medical and social benefits. Learn more at www.lunatechequipment.com.
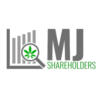
MJ Shareholders
MJShareholders.com is the largest dedicated financial network and leading corporate communications firm serving the legal cannabis industry. Our network aims to connect public marijuana companies with these focused cannabis audiences across the US and Canada that are critical for growth: Short and long term cannabis investors Active funding sources Mainstream media Business leaders Cannabis consumers
No comments so far.
Be first to leave comment below.