Committee Blog: VPD Topics for Cannabis Cultivation and Opportunities to Reduce Facility Energy Costs
Marijuana Laws, Regulations, & Politics February 2, 2023 MJ Shareholders 0
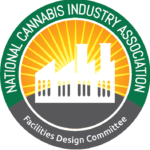
by NCIA’s Facilities Design Committee
Indoor cannabis cultivation facilities are complex environments, where a large number of variables interact to create an ideal ecosystem to grow cannabis. The upside of an indoor facility is it allows a year-long growing climate, optimized for each stage of the plant grow cycle. The downside, however, is creating this ideal climate is very energy-intensive.
There are three (3) main types of precision cooling equipment offered in the cultivation space. Those are Air Cooled DX, Water Cooled DX, and Chilled Water Units. DX stands for direct expansion systems. The immediate and most noteworthy difference between these systems is that DX units cool air using refrigerant, and Chilled Water units cool air utilizing chilled water. A DX unit uses refrigerant-based cooling and cools indoor air using a condensed refrigerant liquid. Typically, the decision regarding which cooling source is better for a cultivation facility is usually driven by the size of the cooling plant as well as other unique site conditions. Selecting the right HVAC system for your cultivation facility can be a challenging process driven by many factors, however this is beyond the topic of discussion for this article, it should be noted that the following analysis assumes an Air Cooled DX based system.
The total energy costs for indoor cannabis grow operations typically vary between 25%-50% of total operating costs (or approximately 150-200 kWh/sq.ft). In comparison, energy use in a typical commercial building environment is approximately 25 kWh/sq. ft. As indoor cultivation facilities increase, they can be a source of strain on electrical grids. A recent study showed indoor cannabis cultivation alone accounted for 4% of the energy grid usage in Denver. (IEEE, 2020)
With that context, any areas we can identify to improve energy efficiencies without introducing a negative impact to the grow environment can have enormous bottom-line impacts for cultivation owners and society at large.
In this article, we are going to be examining two ways we can optimize HVACD systems to improve energy efficiency. When HVACD systems are designed for grow facilities, the primary variables we are looking to influence are the following psychrometric properties: temperature (either wet or dry bulb) and relative humidity. Mechanical engineers will often refer to an information-packed graph called a psychrometric chart shown below.
This chart helps to visualize the relationships different properties of air like temperature, humidity (relative and absolute) and dew points along the saturation curve have with each other. This is useful to analyze, as these are direct inputs to a scientific measure often favored by growers called Vapor Pressure Deficit (VPD).
Vapor Pressure Deficit, simply described, compares these variables to determine how much additional room for water vapor there is in the air. This is important as it determines how readily cannabis plants can transpire. Controlling transpiration rates help to aid in healthy, robust growth through the plant life cycle. Growers tend to want lower VPD, and thus lower transpiration, early in plant maturity, and increase to higher VPDs, and thus high transpiration, at the flowering stage before harvesting.
So we know a successful indoor cultivation facility HVAC system will need to control temperature and humidity to ensure the desired VPD values. How can we do that efficiently?
Stand-Alone Dehumidifiers Are Inefficient
A cannabis plant can transpire up to 99% of the water absorbed through its roots. Due to this, we often tell people that designing an indoor cultivation facility is like designing a data center with a swimming pool inside. Because of the increased humidity introduced from plant transpiration, we must pay special attention to dehumidification strategies within the grow space. Humid air requires treating significant latent loads in the grow space, requiring additional energy to remove moisture from the airstream. This is one reason HVACD systems can consume up to 50% of the energy budget in a cultivation facility. As previously mentioned, higher humidity levels will lower the VPD in the room, preventing a plant from transpiring effectively to continue healthy growth. To combat this, sometimes stand-alone dehumidifiers are added into the grow room.
While these units can do the job of removing moisture from the room, it is a very energy-intensive process. One of the issues with stand-alone dehumidifiers is that they reject heat back into the grow room, thereby adding additional cooling load onto the main HVAC equipment.
Integral Hot Gas Reheat System
An air handling unit, sometimes called an air handler or AHU, is a piece of equipment that is used to condition and circulate air as a component of a heating, ventilating, and air conditioning system.
The air handler is usually a large metal box that contains a blower, heating and cooling elements, filter chambers, sound attenuators, and dampers. It then connects to ductwork that distributes the conditioned air throughout the space before returning it back to the AHU.
Of particular interest are the units cooling coil and reheat coil. These two components are namely responsible for controlling VPD levels in our grow space. In an AHU equipped with Integral Hot Gas Reheat, the cooling coil serves as a dehumidifier, by cooling the air thereby reducing its moisture/latent load (we recommend considering capturing this water for treatment and reuse: read more here). The hot gas reheat capability utilizes heat from grow space and compressor heat to reheat the air before returning to the grow space (without using additional heating energy).
While this may seem like a minor design change, it results in a considerable reduction in energy. As the chart below illustrates, leveraging Integral Hot Gas Reheat units can result in a 30-35% reduction in HVACD energy when compared with other dehumidification systems. Additional automation capabilities built-into these systems will ensure that the grow room will remain tightly controlled within the desired state points of your grow room to optimize VPD.
This reduction in energy quickly adds up to reduced utility bills. Despite marginally higher upfront costs as compared to standard HVAC equipment coupled with standalone dehumidifiers, this option results in a lower 5-year system cost than common HVACD systems installed in cultivation facilities, and these savings will only increase over time.
Maintaining Consistent VPD, but at higher Temperature / Humidity Ranges
The second energy-saving measure we would like to discuss goes back to the earlier discussion of VPD. Recall the equation for VPD is
V P sat – V P air = VPD
This is important, as it provides growers the flexibility to fall within desired VPD ranges, but at higher temperature and humidity ranges than typically used. Many growers target grow room setpoint temperatures around 72-75F and limit relative humidity to a maximum of 50 percent, but by allowing slightly higher room setpoint temperatures of 76-82F, with corresponding relative humidity increases, we can create identical VPDs at higher setpoint temperatures. The cost-benefit of this small adjustment is considerable. The HVAC system (including cooling and dehumidification) can be sized at roughly 20-30% smaller capacity, reducing the owner’s up-front equipment costs. In addition, the system’s energy consumption and costs during operations will be significantly lower, to the tune of 30-40%. In a theoretical 30,000 square foot facility, this could result in $1,125,000 savings in the first 5 years.
The case for a hybrid greenhouse, using VPD controls
Another way of growing instead of full indoor, is a highly efficient, sealed greenhouse. It is designed to maximize sunlight inside the growing environment, meaning energy used for lighting is dramatically reduced. And because it is sealed, energy-efficiency is maximized, as leakage is kept to a minimum. In order to make this work, these greenhouses need to be hybrid (using insulated walls and glazing) and the orientation and design play a bigger role.
In this hybrid greenhouse environment, the growing space typically heats up as soon as the sun comes out, no matter the outside temperature. Cooling in this instance would increase the power usage vs. increasing the humidity to keep the VPD level in the same range. When the sun goes down, the opposite happens. The grow environment starts to cool and it would be expensive to try and keep the temperature up.
In order to achieve VPD control, the control system needs to be able to variably adjust temperature and humidity, based on inputs like weather forecast, time of the day, day of the year, etc. Being able to control the grow environment by VPD level will significantly reduce the energy consumption for your HVACD system.
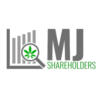
MJ Shareholders
MJShareholders.com is the largest dedicated financial network and leading corporate communications firm serving the legal cannabis industry. Our network aims to connect public marijuana companies with these focused cannabis audiences across the US and Canada that are critical for growth: Short and long term cannabis investors Active funding sources Mainstream media Business leaders Cannabis consumers
No comments so far.
Be first to leave comment below.