Committee Blog: Everything You Wanted to Know About Cannabis Facilities But Were Afraid to Ask Field Guide – Part 1 – Cultivation
Marijuana Laws, Regulations, & Politics April 11, 2022 MJ Shareholders 0
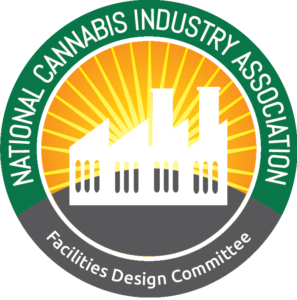
by members of NCIA’s Facilities Design Committee
Jacques Santucci, Brian Anderson, David Vaillancourt, and David Dixon
Introducing our five-part series on the behind-the-scenes workings of the legal cannabis industry. This series focuses on all of the inner dealings and industry advice from established professionals to craft this unlimited How-to-Guide to assist you in setting up your own facility. These articles cover cultivation, extraction, infused products, and retail facilities as well as support activities. In general, remember to be compliant with all local rules and regulations and contact a licensed contractor and industry expert .
Part 1, Cultivation: The Top Things to Consider When Planning Your Cannabis Cultivation Facilities
As you are planning to start your own indoor cultivation facility, there are some often ignored basic parameters that should be taken into account in the design and decision-making process. We have listed the key parameters that will ease the process of going live and may save time and money while you design your facility and the building process. Always remember to be compliant with all local rules and regulations.
- Lighting Recommendations
Depending on your goals, building setting, and local requirements, you have many options for lighting, from HPS light to LED lights. Lighting standards are measured in watts per square foot. Recommendations may vary per state or other criteria. For example, Massachusetts recommends an intensity of 36w/sft for energy consumption.
- Water Recovery: Minimum Percentage
Cannabis is a water-intensive crop, and consideration of effluent capacity can be inefficient, expensive, and an issue for municipalities. Depending on your cultivation practices, you should consider a water recovery system and what percentage you are able to capture. There are two types of water recovery – leachate, and condensate. An effective system will recover at least 70% of the water for utilization, significantly reducing your water and sewer expenses. Your irrigation and fertigation selection will have an impact on your water consumption.
- Generator Capacity: Minimum Recommendations
Your area or your business model may dictate for a generator – which is a critical Business Continuity consideration as a power outage, even if for a brief period of time can destroy a crop. Make sure to calculate the minimum capacity requirements of your facility. Do you plan to have it for emergency or stand-by usage? Typically, 50% of your short lighting load capacity of cultivation, 100% for AHU (air handling), and some back-office and security system, including cameras, access, and server needs.
- Carbon Dioxide Enrichment: New Versus Recaptured
You can consider 75% new tanked- or generated- natural gas and 25% recaptured sources, for cultivation rooms, gas-fired chillers, and gas-fired boilers.
- Carbon Dioxide Alarms Levels: Cultivation and Common Areas
Carbon Dioxide monitoring is critical for worker safety. You should be monitoring common areas to ensure that you are below 3,500 ppm. Monitoring should be tied to the fire alarm system for building evacuation, with 2,000 ppm alarm levels for the cultivation area. 5000 ppm limits are required by NFPA/OHSA. Alarms should contain visual strobes, red/green room access indicator lights and/or possibly an exhaust system that is triggered by an alarm
- Renewable Energy: Minimum Energy Production Percentage
To demonstrate a commitment to sustainability, a minimum target of 10% of your facility’s energy consumption should be from renewable energy production: i.e. solar power, wind energy, geothermal, biomass, and/or battery energy.
- Refuse Disposal: Recycling and Composting
Consider certified disposal of horticulture byproducts with a minimum of 25% recycling or composting by volume; rendered unusable. You will want to establish and verify that your shredder or equivalent system is capable of breaking up debris to a specified size.
- Airlock Doors for In-Between Uses
You should install an airlock barrier, or at a minimum an air curtain, between the business and the production side, for outside and inside egresses, to keep a controlled environment. Keep in mind considerations for ventilation systems and cascading airflow.
- Wall Material
For best performance to mitigate biological hazards and contamination, depending on your region, recommend installing insulated metal panels, that are non-porous, solid core wall, insulated metal panels (IMP), with surface mounted devices.
- Security Entrance: Facility Safety
Consider creating a separate mantrap style entrance to allow for better safety at the entrance point, monitor visitors, keep a controlled environment as well as avoid weather-related issues, i.e. wet areas due to rain or snow, or temperature variance due to extreme heat or cold.
Limiting doors access and key sets for employees needs to be part of your overall security plan, with proper door labeling and authorization levels. The idea is to prevent unauthorized personnel from accessing specific spaces, for proper environment control and to be compliant with the local regulatory body. Remember to be compliant with local rules and regulations.
- Security Camera: Minimum Area of Coverage
In most states, you will need security coverage for 100% percent of your faculty where cannabis products will be stored or displayed, with proper recording and monitoring. Keep in mind that your security room will likely need its own dedicated HVAC systems
- Security Camera: Minimum Data Storage and Resolution
You will need to store all security camera footage on-site for a minimum of 90-days, or more depending on regulations. You may need to store the data offsite for five years for future legal needs. Footage quality may need to be shot in 1080p minimum. An ASTM International Standard Guide for Video Surveillance System provides additional parameters to utilize.
- Security Alarm: Monitoring
Security alarm needs to be monitored by a reputable company. A service level agreement (SLA) or similar to ensure there are redundancies in the event of a failure should be considered, and redundancy or a backup system might be necessary.
- Odor Control: Exhaust Air Management
Odor mitigation is a crucial part of all operations. All exhaust airflow must be oxidized or ionized. You also need a fogger system and carbon filtration. Refer to local municipal bylaws and regulations for more information.
For interior odor control and non-cultivation areas, consider cascading air flows from non-cultivation areas to provide a common method of control for pressurization control. Plan to control air flow and exhaust.
- Fire Sprinkler: Maximum Bench Sizing
Sprinklers are designed to cover a limited surface area. When installed on cultivation tabletops wider than 48”, additional sprinkler coverage may be required.
- Flooring Type: Continuous
Cultivation floors shall have continuous resin or epoxy coating with at least a four-inch lip onto the adjacent wall.
- Energy Incentives: Minimum HVAC/D Efficiency Rating
Air Conditioning (AC) units should be no less than 16 SEER, High Point (HP) units no less than 9 HSPF. Incentives for this vary by state. Please check with your local utility company and regulatory commission for all available rebates.
- HVAC Validation Requirements:
Bi-Annual Third Party Controlled Environment Validation using required Trend Data Metrics is the validation and calibration of control sensors, including temperature, humidity, CO2, and other devices such as scales, flow meters, integral valves, PPM sensors, EC meters, TDS meters, HVAC dampers and other applicable devices that may drift from factory or initial installation specifications.
- Good Agricultural and Collection or Manufacturing Practices (GACP/GMP): Ready Versus Complaint
Your operation should be designed with documentation to prepare for GACP or GMP requirements. Depending on final product types, specific food-based GMPs with appropriate risk assessment programs (such as HACCP, and others referenced within the Food Safety Modernization Act) will prepare you for any federal or international trade opportunities in a federally legalized framework.
- Employee Locker Access
Plan for gender-specific, male and female locker rooms, with six square feet per employee per shift expected to arrive at the facility at any given time. Employee supplied flock for locker or lock provided by the employer is a business decision. Keep in mind how you will keep the environment of your production facility under control. You might consider having locker access adjacent to the growing area with a proper gowning area.
- Locker Room Type
Make sure your locker room is correctly set up for employees to be able to change in a safe way. Specifications for Locker Room and Gowning/PPE Areas should allow access to faucets for washing hands as well as bathrooms. Note gowning areas should be separate from the bathrooms directly off the locker room area.
- Employee Shower Access
Per International Building Code (IBC) and State Plumbing Codes, calculate the number of employees and determine the number of showers based on code requirements as well as business policies. Having gender-specific showers is a recommendation as well as a business decision.
- Emergency Eye Wash- Shower
For safety and based on OSHA standards, Integrated Pest Management (IPM), fertigation, and extraction operations must-have emergency eye wash showers. Eyewash stations need to be placed throughout the facility so that they are within 10-15 seconds walking distance from employees. Check local requirements for additional needs.
Note: in a facility where corrosives and skin irritants could pose harm to employees and require immediate remediations, you should consider emergency showers.
- First Aid Kit Distribution
First aid kits should be available in all rooms where sharp tools and other hazardous materials are intended to be used. These kits need to be within 10-15 seconds of employee walking distances. Per OSHA requirements, first aid kits should be located in all trim, extraction, flower hallway, and shredding areas. This is overall a must-have in your facility.
- Safety and Injury Handling
We recommend that you ensure that you have enough first aid and burn kits available throughout your faculty, based on your activity and the number of employees.
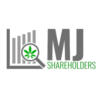
MJ Shareholders
MJShareholders.com is the largest dedicated financial network and leading corporate communications firm serving the legal cannabis industry. Our network aims to connect public marijuana companies with these focused cannabis audiences across the US and Canada that are critical for growth: Short and long term cannabis investors Active funding sources Mainstream media Business leaders Cannabis consumers
No comments so far.
Be first to leave comment below.