Design & Construction Considerations for Cultivation and Processing Operations: Part One
Marijuana Industry News March 19, 2019 MJ Shareholders 0
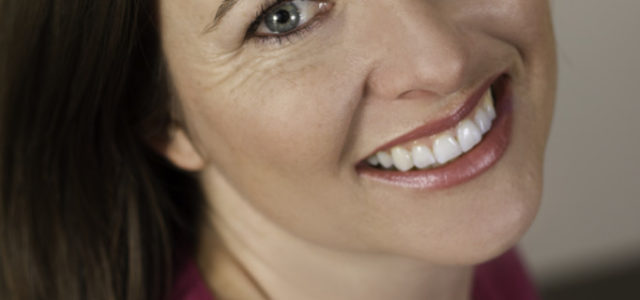
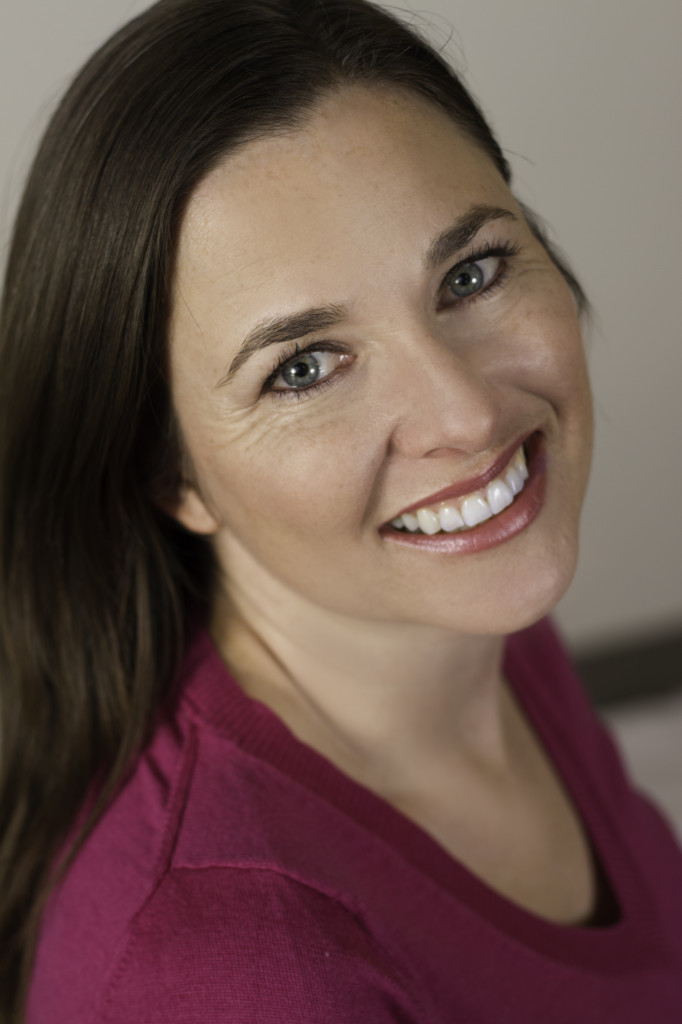
By Laura Breit & Dylan Carey
Process equals product when it comes to designing and building a cannabis cultivation or processing operation. A well-executed design and construction process will result in a well-functioning and well-built facility that will yield great product. All too often, growers and processors go through the process of building a facility and discover – too far down the road – that errors have been made or important steps have been skipped. Mistakes like this can result in major expenditures of both time and capital, and can greatly impact an operation’s bottom line.
The Root Engineers team has broken the design-build process into eight distinct phases: owner decisions, pre-design, schematic design, design development, construction documents, permitting, bidding, and the construction phase. Each of these phases warrant an in-depth exploration to highlight the most important considerations for the design and build of a successful cannabis operation. In Part One of this three-part series, we will discuss the vitally important first phase of the design and construction process, owner decisions.
PHASE 1: OWNER DECISIONS
What is the budget?
One of the most important first decisions an owner needs to make is: what is the budget for building this cultivation or processing facility? This critical piece of information will help decide many factors throughout the design-build process, and assist both the design and construction teams in creating a facility that meets the goals of the operation. Whether your budget is small or large, it is critical to communicate this to your design and construction team. Not doing so can lead to costly and time-consuming redesign efforts.
Who is the Owner’s Representative?
Someone will need to be assigned the role of Owner’s Representative to act on behalf of ownership during site selection, design and construction phases, and operation of the facility. This may be the owner of the company or an employee of the company, although the most successful projects tend to hire an experienced Owner’s Representative. Someone experienced in the construction process will generally pay for themselves when you take into account the efficiency gained having them involved from beginning to end.
Site Selection
The owner and team will need to identify the site or building where the business will operate. Once the site or building is selected, the owner can begin assembling their design and construction teams. Typically, there are two paths a business owner can choose to take when it comes to beginning the design-build process. In the traditional design-bid-build method, an owner will hire separate entities to complete the design and the build – usually a group of designers and, subsequently, a contractor. The design team will complete the design documents and plans, and the owner will then seek out bids from contractors to complete the construction phase based on the design team’s plans. The more modern design-build method involves the owner hiring a single organization to perform both the design and the build of the operation.
There are pros and cons to each approach. The design-bid-build method often has longer timelines and higher upfront design fees. However, this method also results in hard-bid design documents from various contractors, so the owner can feel confident they are getting the best price possible. A design-build path can result in shorter design and construction timelines, as well as a more coordinated process between the design and construction teams, but the costs can be higher overall. Choosing which method is appropriate for a particular project is dependent on the specifics associated with that operation and is best decided by the owner and their business advisors.
An Important Note About Hazardous Operations
When designing and building operations that involve hazardous materials, such as extraction facilities, it’s worth considering enlisting the help of a code expert (architect, engineer, planning consultant, etc) early on in the process to help determine the hazard classifications associated with your business. Having this information and the specific associated requirements prior to purchasing a piece of land or building can save time and money down the road. For example, a building with an H-classified occupancy due to ongoing extraction processes may require a non-combustible building located at least 30 feet from property lines.
By making these important decisions and learning key information at the right times, business owners will set themselves up for success. Stay tuned for Part Two of this three-part series, where we will begin to explore the pre-design, schematic design, design development, and construction documents phases.
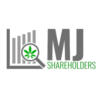
MJ Shareholders
MJShareholders.com is the largest dedicated financial network and leading corporate communications firm serving the legal cannabis industry. Our network aims to connect public marijuana companies with these focused cannabis audiences across the US and Canada that are critical for growth: Short and long term cannabis investors Active funding sources Mainstream media Business leaders Cannabis consumers
No comments so far.
Be first to leave comment below.